
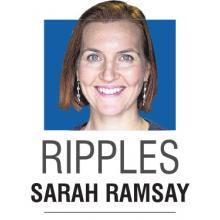
I hear variations of this statement a lot. Generally from people who’ve never met me before, and after such statements most likely never will again.
Let’s unpack how things get made. Imagine you invent the world’s first solar-powered personal MRI machine to diagnose any and all ailments, with the help of Dr Google, from home. You have spent 10 years designing, redesigning and redesigning the redesigns and are finally ready to prototype.
You’ve got investors impatient for results and you’ve overpromised that you’ll have a working prototype at your next meeting. Which is now only six weeks away. You frantically fire your designs off to the local contract manufacturer, only to be told there’s a six-week lead time; you need parts in four weeks so that you have time to assemble and test.
New Zealand manufacturing is hopeless. But is it really?
I don’t understand how it can take years to develop an idea and then completely undervalue the making of it down to a few weeks.
Unfortunately, as CEO of United Machinists we get this a lot with new prototyping work. Particularly from early-stage start-ups or recently graduated product designers who don’t yet understand manufacturing.
So, for my team who every day quietly go about making the impossible, to those at home who are interested in how stuff gets made, through to aspiring industrial designers, here’s a bit of a 101 on how stuff gets made.
CNC machines aren’t microwaves — one of ours is worth over $1 million, that’s a serious piece of kit that only a handful of highly skilled machinists in New Zealand can operate.
We take a designer’s 3-D CAD (computer-aided design) file and import it into our 3-D CAM (computer-aided machining) software — from there our programmers specify every tool, tool path, work holding fixture, operation and spindle speed. They then run a computer simulation, because at up to 18,000 rotations per minute you don’t want to figure out that your machine is going to crash in process.
For really complex multiaxial components, it could take days to programme before it goes near a machine. A highly skilled CNC machinist programmer is a technical role on par with a degree-level qualification (we don’t teach this in New Zealand universities or polytechnics), they don’t just press start-stop buttons.
Fast isn’t better — ever walked past an empty restaurant and kept on going, only to wait a bit longer at the place next door that’s cranking? That’s because you assume the busy restaurant is better, right?
Machine shops, particularly those at the advanced end of the spectrum, are highly capital-intensive businesses that need to keep their spindles running. Being busy is a sign of a good machine shop, being able to give accurate schedule forecasts is an excellent one.
On average to make a part first time we’ll buy material (three days), programme and prove the job (three days), manufacture any custom fixtures (two days), machine the part across multiple operations (five days), arrange any surface treatment processes such as anodising (five days) and undertake in-process and final inspections (two days).
The last step often uses specialised measuring equipment to measure tolerances as tight as 6 microns (for the layman geeks like me a human hair is about 75 microns, so we’re machining tolerances less than a 10th of a human hair).
So for an entirely new prototype we are looking at 20 business days to comfortably work through the first production run. Allowing for a four-week forward schedule, eight weeks is realistic.
New Zealand is an island at the bottom of the world — if you are specifying exotic materials or special features it’s highly likely we’ll need to air freight the raw material or special tools in from Europe or the US. This isn’t cheap or fast.
We recently quoted a job that required special-grade aluminium from Europe, lead time is three-four months, due to the current shipping crisis in the Suez Canal.
Many designers incorporate special surface finishes or colours that aren’t readily available anywhere in Australasia and have mixed repeatability when sourced from overseas.
We will often get design features that are impossible to achieve with common tooling and processes. If you don’t need the complexity, design it out, which will remove inherent risk in the design, fit domestic capability and make it more commercial and faster to manufacture.
Partner with your manufacturer — take the time to meet around a design release and be open to design for manufacturing feedback. New Zealand specialises in low-run, high-value, high-mix production. Which means our talented engineers, machinists and technicians have made thousands of different parts and have a wealth of knowledge.
At United we’ve had fantastic wins in optimising the efficiency of design, in many cases making recommendations that will allow a component’s manufacture to be automated or fixtured for multiple parts at once, removing significant cost. If we can design this into the initial prototype run, it’s set up for repeatability and volume efficiencies from day 1.
The good/fast/cheap rule is not new. Society has been trained to value fast and cheap more and more in our everyday lives.
Perhaps we need to incorporate a fourth metric to the rule, "sustainable" — because if you are getting good, fast and cheap, then someone or something else is definitely paying for it.
If we value the makers, then we can work in partnership together and invest in building more sustainable and advanced capability for New Zealand.
- Sarah Ramsay is CEO of United Machinists.