
Knowing they are literally giving people a helping hand is a thrill for the team at United Machinists.
The Dunedin engineering firm has a partnership with Taska Prosthetics to produce internal components for the Christchurch-based company's prosthetic hands.
It was the first and only firm to achieve production volumes for those components. Had they not been able to, it was "highly likely" manufacturing would have had to go offshore, United Machinists commercial director Sarah Ramsay said.
Taska was exporting the world's first waterproof and robust myoelectric multi-articulating prosthetic hands to Australia, the United States and Europe.
United Machinists has added two machines - a vision co-ordinate measuring machine (CMM) and semi-automated twin spindle lathe DMG Mori NLX 2500, worth more than $500,000 in total, especially for Taska.
The CMM could measure down to 0.003 of a millimetre or three micron; once the parts were manufactured, they were run through the CMM to ensure they were within tolerance - some intricate parts had up to 15 different dimensions to measure.
Essentially those parts were the "gearboxes" in each knuckle of the hands and United made about 16 components for each hand.
When they did a catch-up with staff about what they loved most about their jobs, being able to make a real difference to people's lives was commonly mentioned, Ms Ramsay said.

"Obviously, Mat's injuries weren't as serious as those faced by some of our users, but that experience led to the realisation that the upper-limb prosthetics market was not well served at the time and that he could do much better," chief executive Jamie Cairns said.
There was now a team of more than 35 people in design, research, engineering and commercial areas at Taska.
The company's success had been driven by a desire to improve the lives of upper-limb amputees by reducing the compromises being made in product design and manufacture.
The Taska hand was highly sensitive and agile. It had sensors to detect muscle movement to control the hand as well as its own app and electronic interface to fine-tune and preset hand positions, making tasks such as peeling potatoes a reality.
United Machinists was established in Dunedin in the 1940s and it was bought by Doug and Lesley Ramsay more than 40 years ago.
It is now run by their son Alex Ramsay, who is managing director, while his wife and co-owner Sarah joined the business formally as commercial director earlier this year. There are 16 staff.
The Taska partnership had been a "massive" learning curve but also real validation for the team, Mr Ramsay said.
"We had the guys trained in a week and we were producing components by the second week," he said.
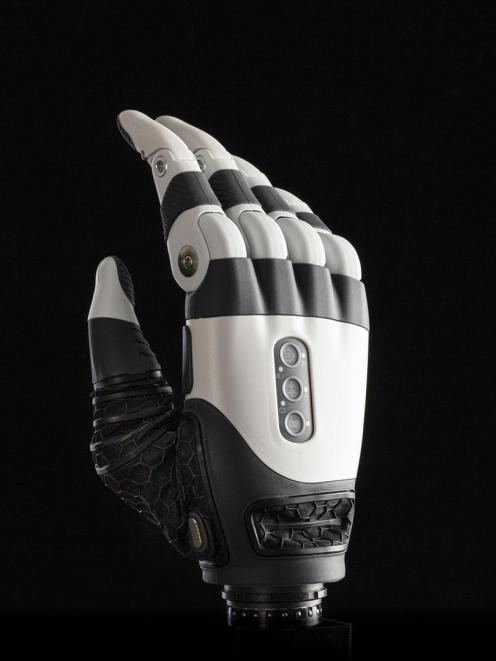
"It's the kind of work you dream of when you train to be a machinist," he said.
The firm's work used to be more industrial but now was increasingly hi-tech, including work for Queenstown-founded Shotover Camera Systems which makes high-performance aerial camera systems for the motion picture and broadcasting industries, featuring in some of the world's biggest blockbuster movies.
When the couple bought the business, it was with the intention of repositioning it to specialise in high-tech manufacturing, Mrs Ramsay said.
Everything they had invested into processes and systems and upskilling both their team and themselves was paying off. Productivity, profitability and on-time delivery had all gone up, she said.
Probably their biggest constraint to growth was labour and one of their "bugbears" was the industry not being promoted to school leavers.